Nos engagements
Diminuez votre coût €/tonne et votre empreinte carbone :
Grâce aux engagements EXPLOROC, faites d’une pierre deux coups !
La fiabilité et la répétabilité des résultats techniques
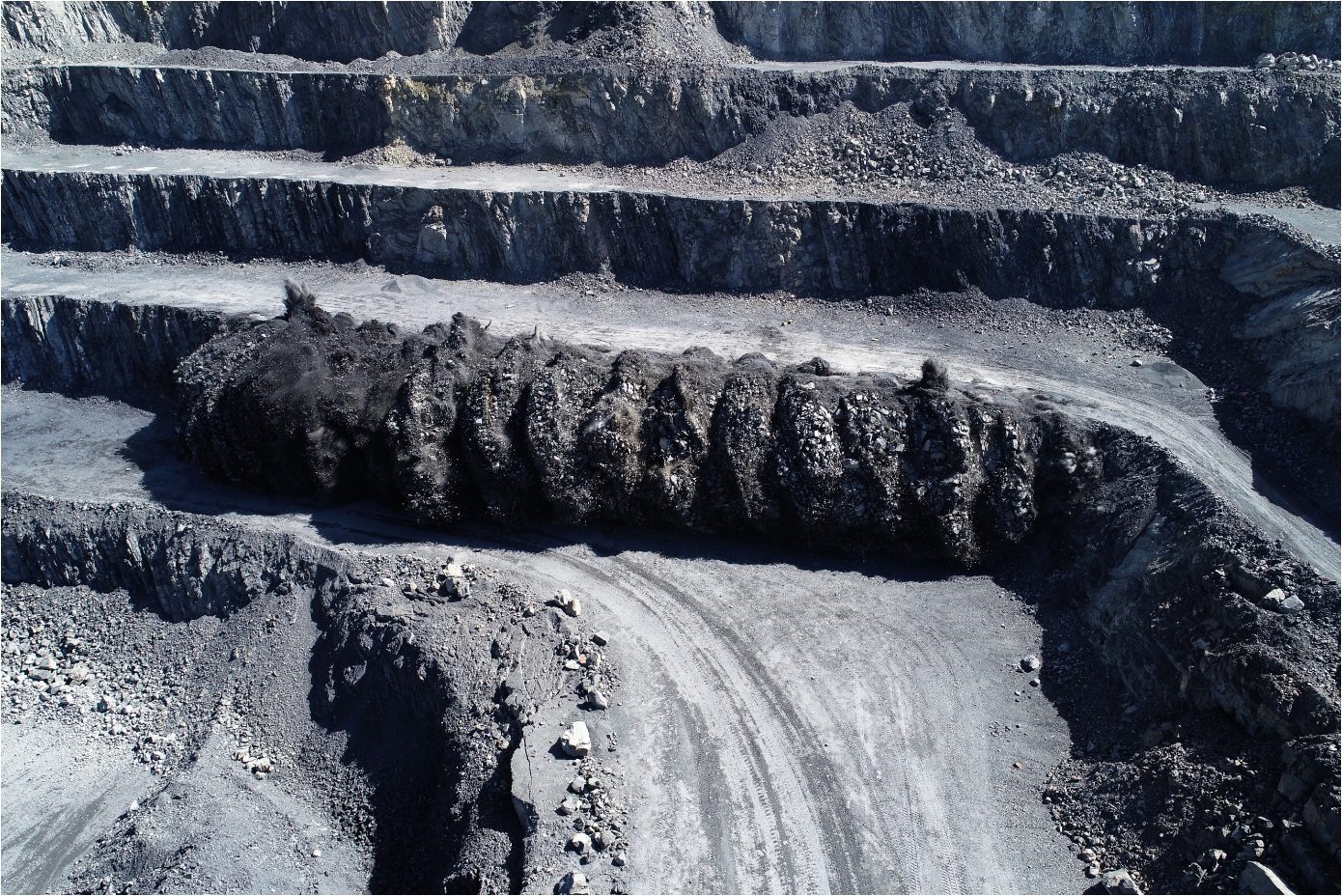
L’ensemble des procédures instaurées assure une exploitation et une valorisation maximales du gisement.
Nos garanties commerciales
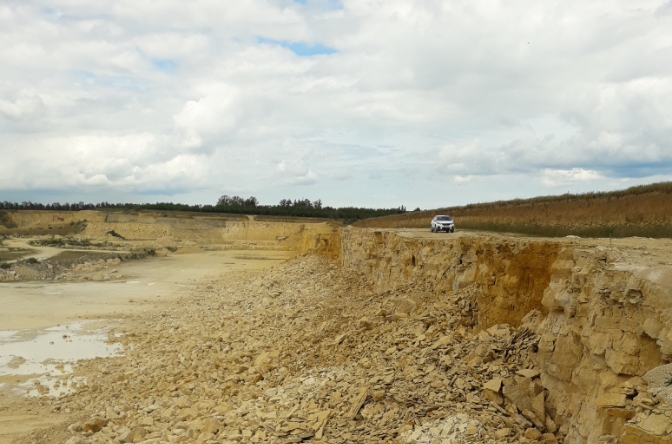
EXPLOROC s'engage sur une granulométrie maximale adaptée au concasseur utilisé et un pourcentage de blocs. Cet engagement s'entend généralement sur un volume global annuel. En cas de dépassement :
- Estimation tir par tir du taux de blocs constaté
- Prise en charge financière des heures de pelle BRH pour casser les volumes en dépassement par rapport à l’objectif initial
- En option : cet engagement peut s'entendre tir par tir.
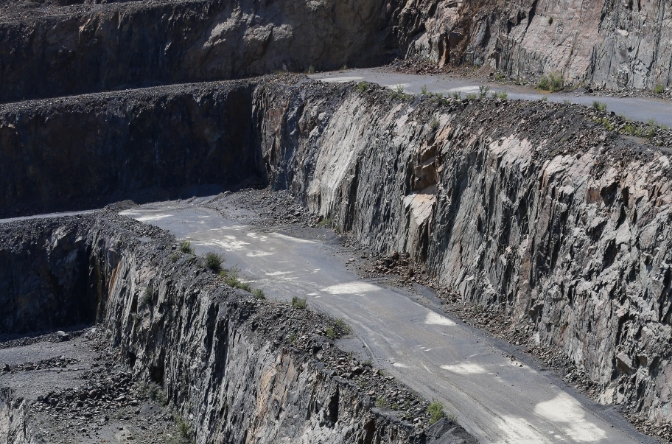
EXPLOROC assure le suivi en Z des carreaux minés. En cas de point supposé au-dessus de plus de 70 cm par rapport à la cote minée :
- Contrôle topographique à la charge du mineur, même si ce contrôle est un cabinet extérieur missionné par l’exploitant
- Traitement à la charge d'EXPLOROC, dès la prochaine intervention
- En option : une pénalité de 2000 € par mois de retard de traitement peut être appliquée.
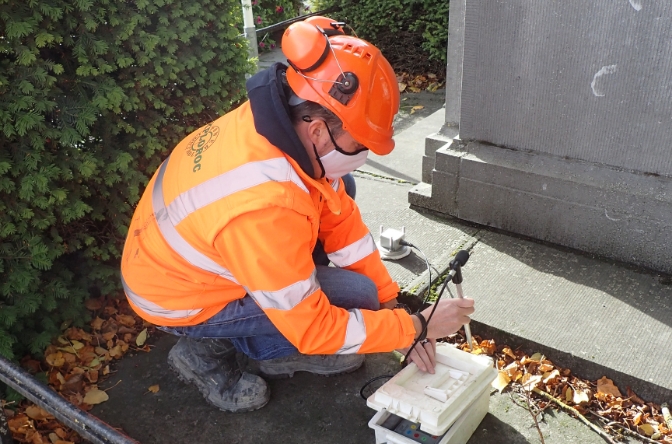
EXPLOROC s'engage à respecter les contraintes vibratoires définies par le client en fonction des arrêtés préfectoraux et des contraintes locales. En cas de non- respect de la norme vibratoire prévue :
- Un seuil supérieur de tolérance de 1 mm/s de dépassement est appliqué, donnant lieu à un plan d’action correctif de la part d’EXPLOROC.
- En option : au-delà de ce seuil de tolérance de dépassement de 1 mm/s, un montant forfaitaire de 15% de retenue sur facture peut être appliqué.
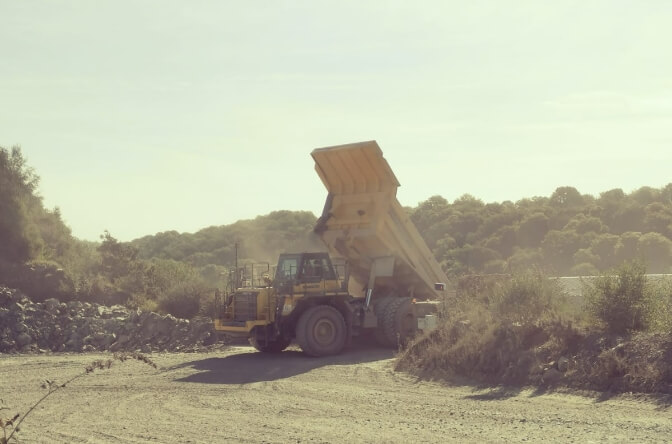
+10% en moyenne
EXPLOROC réalise au début de son intervention un diagnostic de la productivité du site, et met en oeuvre des moyens pour optimiser la cadence du concasseur primaire, dans les limites des autres objectifs fixés.
- Le gain moyen sur les cadences d'extraction est de 10% par rapport à la situation initiale.
- En option : un système de bonus/malus peut être mis en place, basé sur les indicateurs fournis par le client.
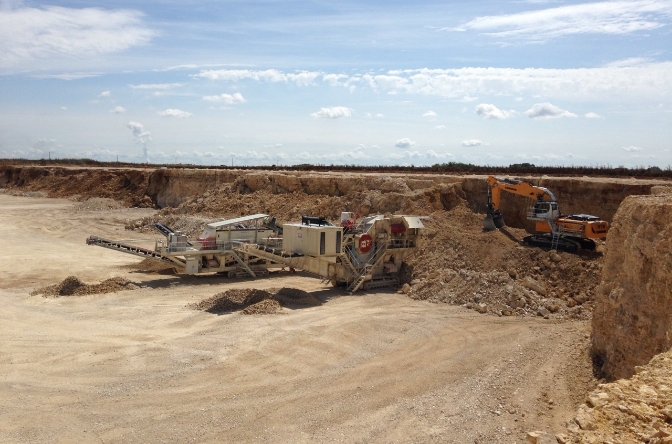
-15% en moyenne
EXPLOROC met en oeuvre des moyens pour optimiser le taux de stérile du gisement, dans la limite des autres objectifs fixés.
- La méthodologie EXPLOROC permet généralement de baisser le taux de stériles de 15% par rapport à la situation initiale (par exemple 17% au lieu de 20%).
- En option : un système de bonus/malus peut être mis en place, basé sur les indicateurs fournis par le client.
Nos engagements RSE
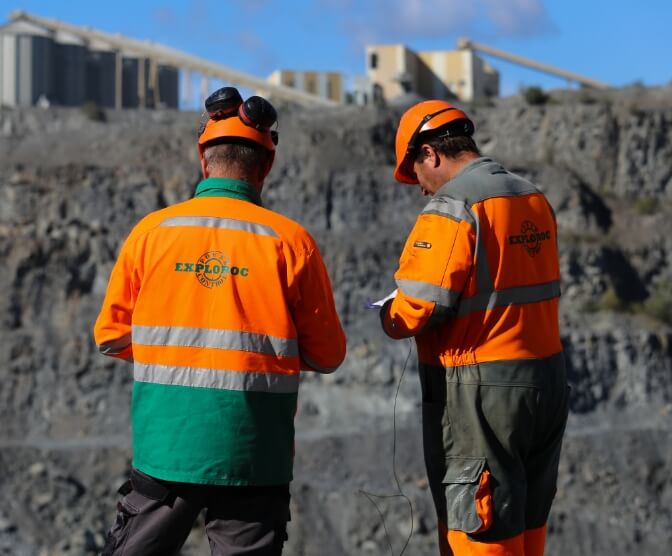
Même si le risque zéro n'existe pas en matière de foration / minage, nos procédures internes vous garantissent de minimiser les risques à tout moment dans votre exploitation :
- Contrôle d'implantation et des plans de foration
- Foration fond de trou systématique pour une parfaite rectitude de trous
- Implantation en 3D, x,y et z pour une maîtrise des hauteurs de chargement et une adaptation fine des paramètres de tirs
- Implantation des trous à 3 mètres de la crête pour limiter les risques de chute
- Contrôles d'épaisseurs de banquette systématiques en première rangée à la sonde TEPEX
- Formation et stabilité des nos équipes
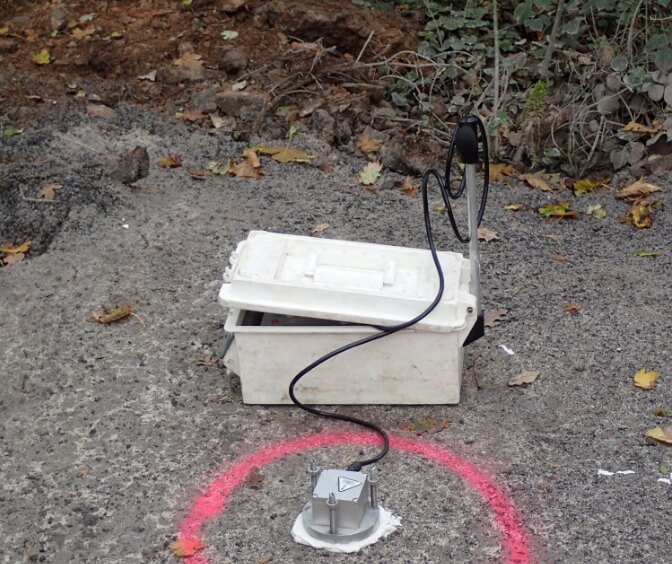
Par une analyse approfondie des coefficients K de votre gisement, des types et des séquences d'amorçage et par un plan de chargement adapté, nous mettons tout en œuvre pour respecter de façon drastique votre contrainte en matière de seuil de vitesse de vibrations et de surpression aérienne.
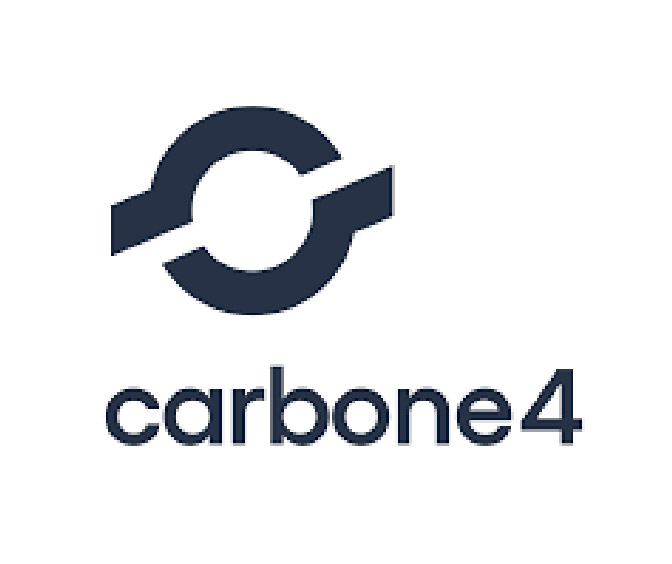
Au travers d'un accord cadre mis en place en 2021 avec le cabinet d'étude spécialisé Carbone 4, nous sommes en mesure de vous proposer une approche approfondie de l'impact carbone lié à votre activité minage et à l'extraction des tirs. Une exclusivité Exploroc.
L’esprit de service
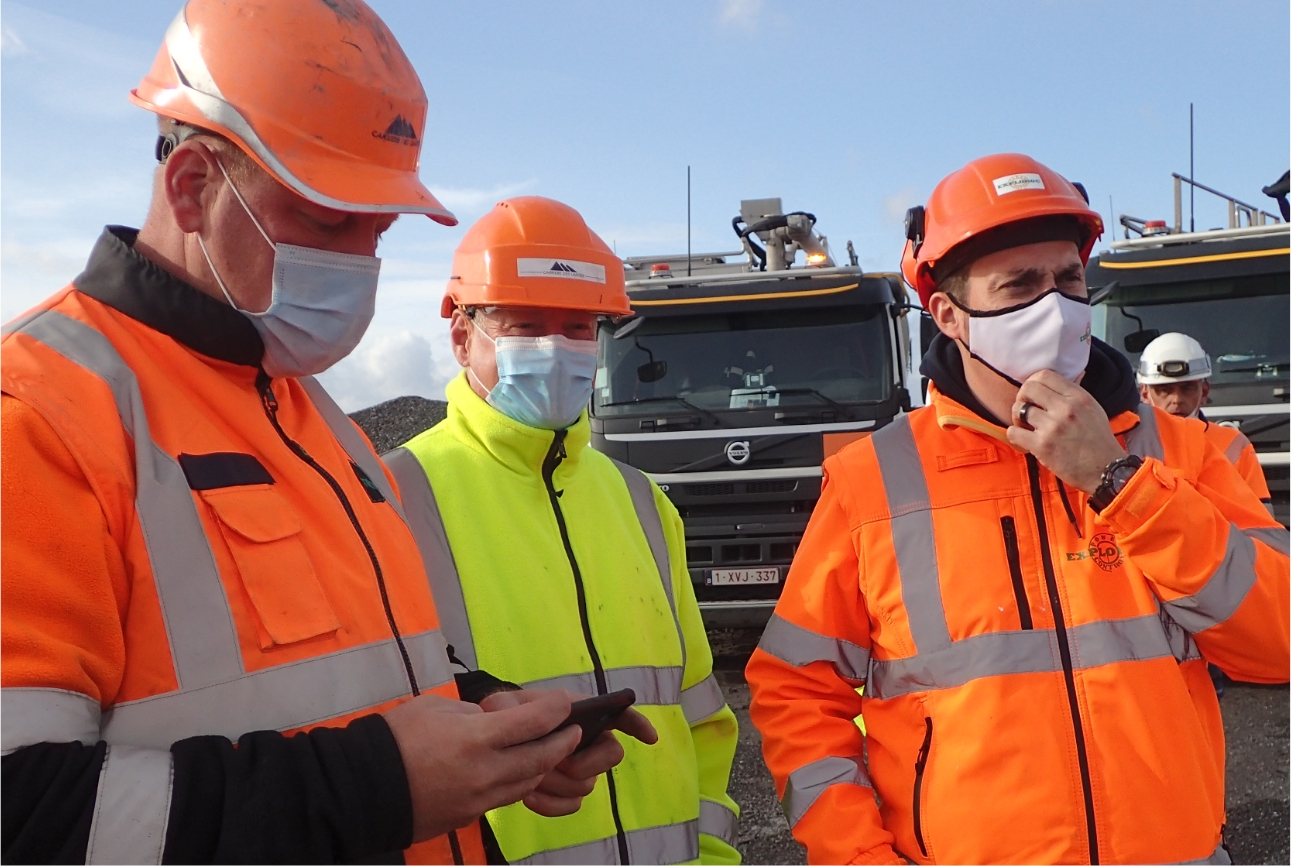
L’esprit de service dans la relation client, grâce à la formation permanente de nos équipes et leur fidélisation dans la durée.